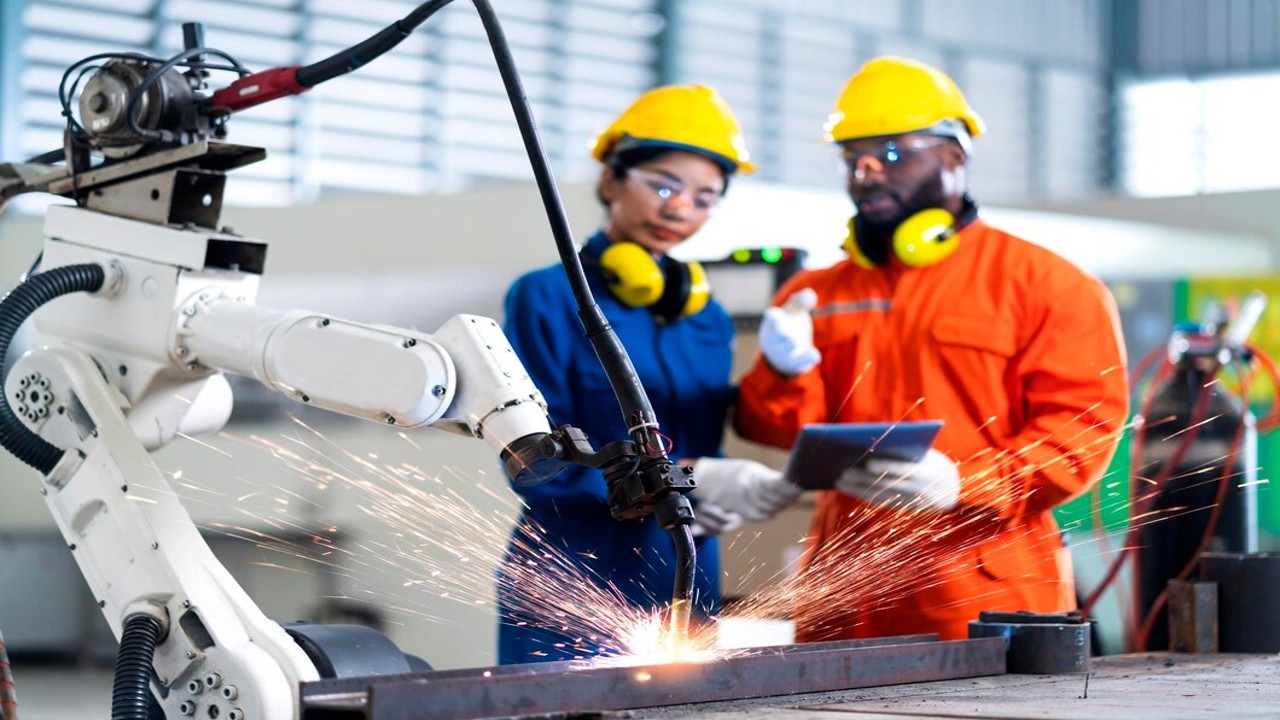
Industrial operations form the bedrock of economic activity, driving the production and distribution of goods essential for societal growth. Within this landscape, the quality of equipment and the effectiveness of maintenance support are paramount for ensuring seamless operations. Bendtech Defence stands out as an exemplary leader in this regard, implementing best practices to optimize efficiency and reliability. Through prioritizing high-quality equipment and implementing proactive maintenance strategies, a benchmark for excellence in industrial operations is established.
Contents
Quality Equipment: The Lifeline of Industrial Operations
Quality equipment stands as a pillar supporting industry operations. Without it, the productivity, efficiency, and safety of these operations come under threat. Investing in high-standard machinery and tools ensure not only the durability of equipment but also aids in minimizing the costs associated with damages and downtime.
Industries like manufacturing, construction, shipping, and defence, to name just a few, depend on a wide array of equipment. These range from simple hand-operated devices to complex machinery. The broad spectrum of tools used poses a direct correlation to the quality of the output. It is, therefore, of essence to ensure the equipment is of superior quality. High-quality tools tend to be more reliable, reducing the chances of sudden operational failure and hence, downtime in industrial operations.
Maintenance: A Key Aspect of Industrial Operations
While quality equipment lays the foundation for successful industrial operations, maintenance support is often the factor between failure and success, especially in the long term. Ignoring the importance of regular and thorough maintenance can lead to frequent machine failures, production stoppages, and even possible safety risks for the operators.
A robust maintenance support system offers a host of benefits. It enhances the equipment’s lifespan, results in reduced operational costs, and ensures a safer working environment. Scheduled maintenance check-ups can also identify potential issues at an early stage, preventing severe damage and elongating the life of the equipment.
Best Practices: A Model for Industrial Operations
An embodiment of best practices in utilizing quality equipment and maintenance support for optimizing industrial operations can be found with a company in the defence industry. They are well-recognized for their commitment to quality and precision, making them a leading name in their sector.
This company operates on the principle of ensuring only the best-quality equipment is utilized in their production processes. This has resulted in end products that meet rigorous quality standards and operational efficiency. Their emphasis on comprehensive maintenance support, including regular check-ups and swift problem-solving efforts, have reduced downtime significantly, enabling them to meet project deadlines efficiently.
The Importance of Training
Investing in quality equipment and robust maintenance support is half the battle. To fully leverage the capabilities of equipment, training and knowledge development of the operating personnel are crucial. High-level machinery often requires specialized handling. Without proper training, the advantages of such equipment might not be fully realized due to inadequate or incorrect use. Thus, on-the-job training and workshops should be an integral part of industrial operations.
Integration of Technology: Revolutionizing Industrial Operations
In today’s rapidly evolving industrial landscape, the integration of cutting-edge technology stands as a pivotal factor in optimizing operations. From automation and data analytics to predictive maintenance systems, technological advancements have revolutionized the way industries operate. Embracing technology not only enhances efficiency but also drives innovation, ultimately leading to greater competitiveness in the market.
Incorporating state-of-the-art technology into industrial equipment brings forth numerous advantages. Automation, for instance, streamlines processes, reduces human error, and boosts productivity. Moreover, with the advent of the Internet of Things (IoT), machinery can now communicate real-time data, allowing for predictive maintenance measures to be implemented effectively. This proactive approach minimizes downtime and prevents costly equipment failures, ensuring uninterrupted operations.
The Connection Between Quality Equipment and Maintenance Support
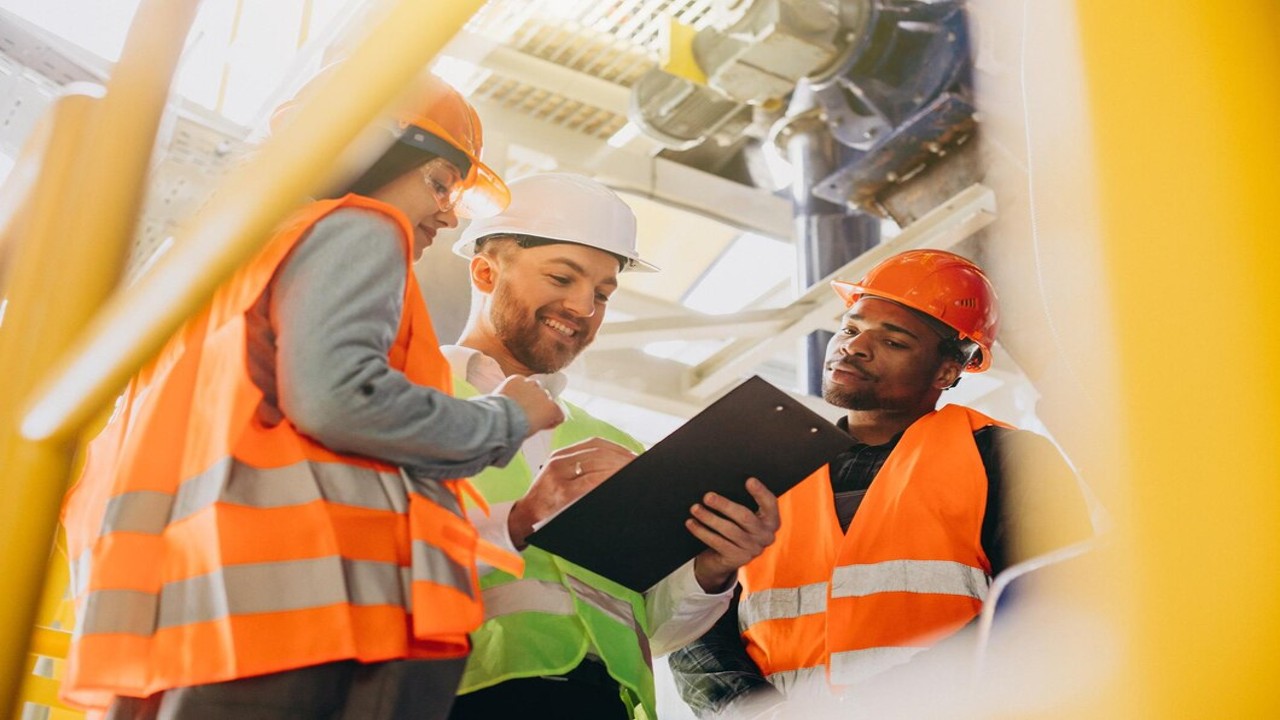
The marriage of quality equipment and robust maintenance support is a harmonious one that yields great results in optimizing industrial operations. Quality equipment ensures high productivity levels and safety, while consistent maintenance leads to the longevity and reliability of said equipment. The two factors together allow for streamlined operations with minimal disruption, resulting in a more economically viable and effective business model.
The role of quality equipment and maintenance support can never be overstated in the context of industrial operations. It forms a triad with human resources, making up the backbone for any successful industry operation. The strategy should be to invest in high-quality equipment initially, complemented by solid maintenance practices and continuous personnel training. Such an approach might seem cost-intensive initially, but it saves substantially in the long run by averting costly repairs and extensive downtime.
Final Thoughts
It is fitting to conclude on the note that the key to optimizing industrial operations lies in recognizing and capitalizing on the benefits of quality equipment and dedicated maintenance support. Empowerment of these factors can deliver a formidable impact on the efficiency and continuity of production, pushing industrial operations optimisation to unimaginable bounds.