Concrete is a fundamental building material used in construction projects worldwide. It provides durability and strength to structures, making it a crucial component in the construction industry. However, in some cases, concrete may exhibit a phenomenon called Segregation of Concrete, which can lead to compromised structural integrity. In this article, we will delve into the causes, effects, and preventive measures related to Segregation of Concrete.
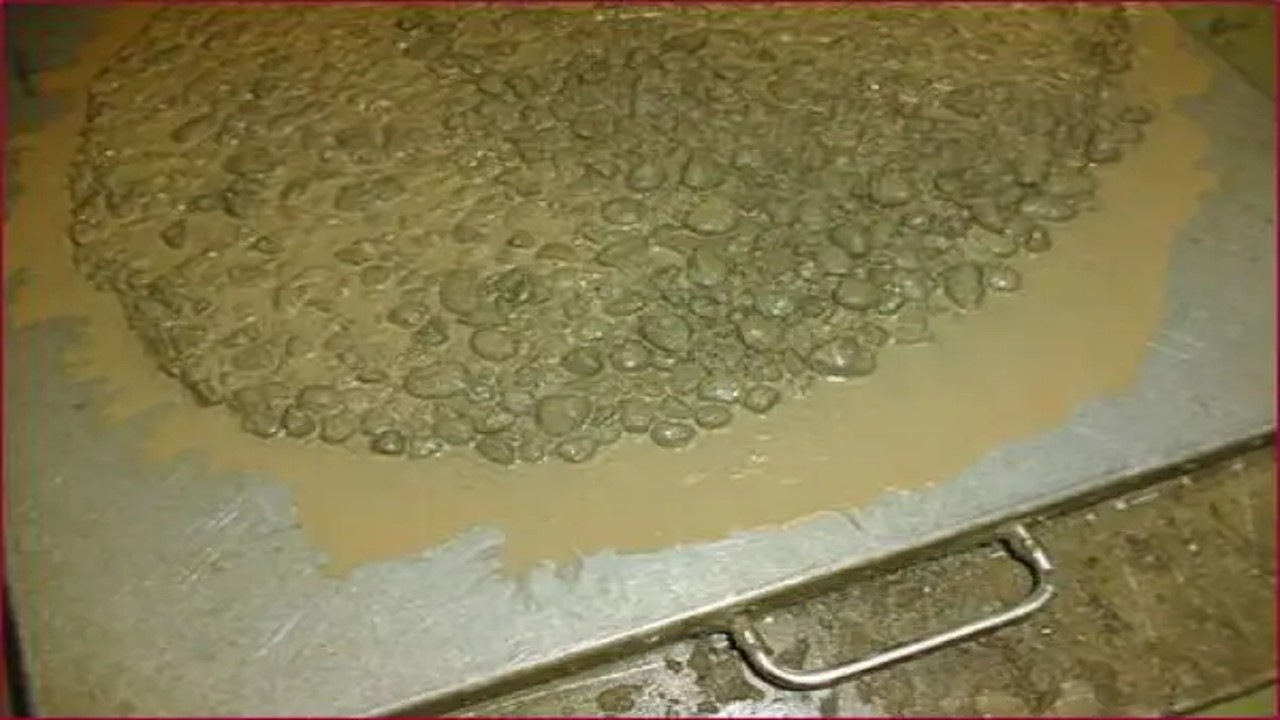
Contents
Introduction
Concrete is the backbone of modern construction, offering strength and stability to various structures. However, sometimes, during the mixing and placing process, a phenomenon known as concrete Segregation of Concrete can occur, leading to a less-than-optimal final product. Understanding the causes, effects, and ways to prevent Segregation of Concrete is crucial for ensuring the quality and longevity of construction projects.
What is Segregation of Concrete?
Segregation of Concrete refers to the separation of the components within a freshly mixed concrete mixture. Concrete is composed of various materials such as cement, aggregates (like sand and gravel), water, and sometimes admixtures. When the concrete mixture is not properly mixed or handled, these components can separate, leading to an uneven distribution of materials.
Types of Segregation of Concrete
Bleeding
This occurs when water in the concrete mixture rises to the surface due to the settling of solid particles. It can result in a layer of water on the surface, weakening the top layer of concrete and potentially causing cracking.
Settlement
If the concrete mixture is not properly compacted or vibrated, heavier aggregates can settle at the bottom, leaving a higher concentration of cement and water at the top. This can lead to a non-uniform distribution of strength and properties within the concrete.
Sand streaks
Improper mixing can cause sand and coarse aggregates to separate from the cement paste. This can create streaks of different materials on the surface of the concrete.
Segregation at edges
During transportation and pouring, the heavier aggregates can settle at the edges, leaving a weaker mix at the center. This can lead to an uneven appearance and compromised structural integrity.
Segregation of Concrete can result in a number of problems, including reduced strength, durability, and overall quality of the concrete. To prevent Segregation of Concrete, proper mix design, handling, transportation, and placement techniques are essential. Adequate mixing and proper use of vibration tools during placement help ensure a homogeneous distribution of the materials within the mixture.
Causes of Segregation of Concrete
Segregation of Concrete can occur due to various factors, many of which are related to improper mixing, handling, and placement practices. Here are some common causes of concrete segregation:
Particle Size and Grading
Aggregates in concrete come in various sizes, from fine sand to coarse gravel. If the aggregates are poorly graded or the particle sizes are not properly proportioned, they can separate during mixing and placement, leading to areas with higher concentration of finer particles and vice versa.
Bleeding and High Water Content
When there’s an excess of water in the concrete mix, it can lead to bleeding, where water rises to the surface due to the settlement of solid particles. As water comes to the top, it carries finer particles with it, leaving the coarser aggregates behind. This can result in weaker, less durable concrete at the surface.
Improper Mixing
Inadequate mixing, whether due to insufficient mixing time or improper equipment, can cause poor dispersion of cement particles and aggregates. This can lead to clumps of aggregates settling together and areas with inadequate cement paste.
Vibration Technique
Vibrating concrete is crucial to remove air bubbles and achieve proper compaction. However, improper use of vibrators, such as over-vibrating or not using them consistently, can cause heavier aggregates to settle at the bottom and result in areas with less coarse aggregates and more cement paste.
Free Fall Height
When concrete is allowed to fall from a height during pouring, it can separate due to the impact. Heavier aggregates tend to move downward, while finer particles rise. This is particularly problematic for larger aggregates.
Long Hauling
Transporting concrete over long distances can cause segregation. Agitation and movement during transportation can lead to separation of aggregates, with heavier particles settling and lighter particles rising.
Formwork Design and Pouring
Inadequate formwork design or turbulence during pouring can lead to segregation. Poorly designed formwork can cause disruption in the flow of concrete, leading to separation of materials.
Inadequate Compaction
If the concrete is not properly compacted after placement, voids and pockets can form where aggregates have separated from the cement paste. This can result in weak points in the structure.
High Slump and Workability
While a certain amount of slump is necessary for concrete workability, excessive slump can cause segregation. Overly fluid concrete can lead to the separation of heavier aggregates from the paste.
Inadequate Handling
Aggressive handling of concrete, such as dropping it from a height, can lead to particle separation. Using improper tools or shoveling too forcefully can exacerbate the problem.
Addressing these causes involves careful mix design, proper equipment and tool usage, appropriate handling techniques, and meticulous attention to detail during all stages of concrete preparation, transportation, and placement. Preventing Segregation of Concrete is important to ensure the structural integrity and durability of concrete structures.
Effects of Segregation of Concrete
Segregation of Concrete can have a range of negative effects on the properties, strength, durability, and aesthetics of a concrete structure. Here are the detailed effects of Segregation of Concrete:

Reduced Strength
Segregation of Concrete can lead to uneven distribution of cement paste, aggregates, and other components. This non-uniform mixture results in areas with insufficient cement paste, leading to lower compressive strength and decreased load-bearing capacity of the concrete.
Poor Durability
Areas of low cement content due to Segregation of Concrete are more susceptible to cracking, weathering, and deterioration. These weakened zones are prone to water infiltration, freeze-thaw damage, and chemical attack, which can significantly reduce the overall durability of the structure.
Surface Blemishes
Segregation of Concrete often results in an uneven appearance on the surface of the concrete. Harsh lines between areas with different concentrations of aggregates and cement paste can create an aesthetically displeasing surface with patches of varying textures and colors.
Inadequate Bonding
Segregated areas may have a weaker bond with adjacent properly mixed concrete, leading to reduced structural integrity. This is particularly concerning for reinforced concrete elements, as the weakened bond can compromise the load transfer between concrete and reinforcing bars.
Cracking
Segregation of Concrete can contribute to the formation of cracks, especially at the interfaces between segregated zones and areas with proper mix distribution. These cracks can allow moisture and contaminants to penetrate, accelerating deterioration.
Uneven Hardening
Segregated areas tend to have different curing conditions due to variations in moisture content and cement paste distribution. This can result in uneven hardening and incomplete hydration of cement particles, leading to compromised strength development.
Surface Dusting
In areas where fines (smaller particles) have segregated to the surface, the concrete can become more porous and prone to dusting. This occurs when the surface layer weakens and disintegrates, releasing fine particles into the air.
Weak Points in the Structure
Segregation can create weak points that reduce the overall load-carrying capacity of the structure. These weak points can lead to localized failures and compromises in structural integrity, potentially endangering the safety of the structure.
Reduced Workability
While some parts of the concrete mix may become overly fluid due to segregation, other parts can be too dry and difficult to work with. This inconsistency in workability can hinder proper placement and finishing.
Aesthetic Concerns
The uneven surface appearance caused by segregation can detract from the visual appeal of the concrete, especially in architectural and decorative applications. This can lead to dissatisfaction with the final appearance of the structure.
To mitigate the negative effects of concrete segregation, it’s crucial to implement proper mixing techniques, careful handling, appropriate vibration methods during placement, and adequate curing practices. Quality control measures should be in place to ensure that the concrete mixture remains well-distributed, resulting in a strong, durable, and visually appealing finished product.
Prevention of Concrete Segregation
Preventing Segregation of Concrete requires a combination of careful mix design, proper handling and placement techniques, and quality control measures. Here are the detailed steps to prevent concrete segregation:
Proper Mix Design
1. Use well-graded aggregates to ensure a balanced distribution of particle sizes.
2. Adjust the proportions of cement, water, aggregates, and admixtures according to the specific requirements of the project.
3. Opt for low-slump mixes when feasible, as excessively high slump can increase the likelihood of segregation.
Controlled Water Content
1. Use the minimum amount of water required for workability to prevent bleeding.
2. Avoid adding extra water during mixing or placement.
Effective Mixing
1. Use well-maintained and appropriate mixing equipment to ensure thorough dispersion of materials.
2. Mix the concrete for a sufficient duration to achieve uniform consistency.
Optimal Vibration
1. Use vibrators to ensure proper consolidation of the concrete during placement.
2. Apply vibration evenly and consistently to minimize the risk of aggregates settling.
Proper Placement Techniques
1. Use chutes, hoppers, or other equipment that minimize the distance the concrete falls during placement.
2. Avoid allowing concrete to free-fall from heights, as this can cause segregation.
Reduced Transport Distances
Minimize the distance that concrete needs to be transported to prevent excessive agitation and potential segregation.
Formwork Design and Pouring
1. Ensure formwork is properly designed to allow smooth and uninterrupted flow of concrete.
2. Avoid turbulence during pouring by using proper pouring techniques.
Controlled Slump
Use slump tests to determine the appropriate consistency of the concrete mix. Maintain a manageable slump without excessive fluidity.
Careful Handling
Handle concrete gently to avoid causing separation of materials. Use tools that aid in proper placement without excessive disturbance.
Quality Control
1. Implement rigorous quality control procedures to monitor the mixing and placement process.
2. Conduct slump tests, air content tests, and other relevant tests to verify the concrete’s properties.
Immediate Finishing
Begin finishing operations as soon as possible after placement to prevent segregation at the surface.
Proper Curing
Ensure proper curing practices to maintain consistent moisture levels throughout the concrete, promoting even hydration and strength development.
Temperature Considerations
Adjust mix proportions and placement techniques based on ambient temperature to prevent rapid drying and segregation.
Educated Workforce
Train workers and construction personnel on proper handling, placement, and finishing techniques to minimize the risk of segregation.
Admixtures
Use admixtures designed to improve workability and reduce the risk of segregation, such as high-range water-reducing agents (superplasticizers).
By incorporating these prevention measures, construction professionals can significantly reduce the risk of concrete segregation. A well-mixed, properly placed, and adequately cured concrete mixture will result in a durable and structurally sound finished product.
Watch Reference Video
Source: Engineering Motive
Conclusion
Segregation of Concrete can significantly impact the quality and longevity of construction projects. By understanding the causes, effects, and preventive measures associated with segregation, contractors and engineers can take proactive steps to ensure the structural integrity, aesthetic appeal, and durability of their creations.
Frequently Asked Questions (FAQs)
How does excessive water content contribute to Segregation of Concrete?
Excessive water weakens the cement paste, causing heavier aggregates to sink and water to rise, resulting in segregation.
Can segregation be visually identified?
Yes, Segregation of Concrete often leads to non-uniform surfaces and variations in color and texture, making it visually distinguishable.
Is Segregation of Concrete reversible once it occurs?
No, once segregation occurs, it cannot be reversed. However, preventive measures can minimize the risk of its occurrence.
How can contractors prevent concrete segregation?
Contractors can prevent segregation by using proper mix designs, mixing techniques, controlling water-cement ratios, and employing adequate vibration during placement.