In today’s post, we will learn Why does RCC slab cracks after one day of casting. Many people have convictions that after slab casting, why does hair cracks develop in the slab. How can this be stopped? So to clarify this confusion of you people, I am going to illustrate the Top 10 reasons, which will make your confusion go away. So let’s start.
An RCC slab refers to a reinforced concrete slab, which is a common structural element used in buildings and other construction projects. RCC stands for Reinforced Cement Concrete.
RCC slabs are horizontal elements that provide a sturdy and flat surface for floors, roofs, balconies, or any other area that requires a solid structural platform. They are designed to support the loads imposed on them, such as the weight of people, furniture, equipment, and other applied loads.
RCC Slab Construction involves the following steps
- Design: The slab is designed based on the structural requirements, including the span (distance between supports), the loads it needs to bear, and any other specific considerations.
- Formwork: Formwork is set up to create the desired shape and dimensions of the slab. It typically consists of wooden or metal frames and panels that hold the wet concrete in place until it hardens.
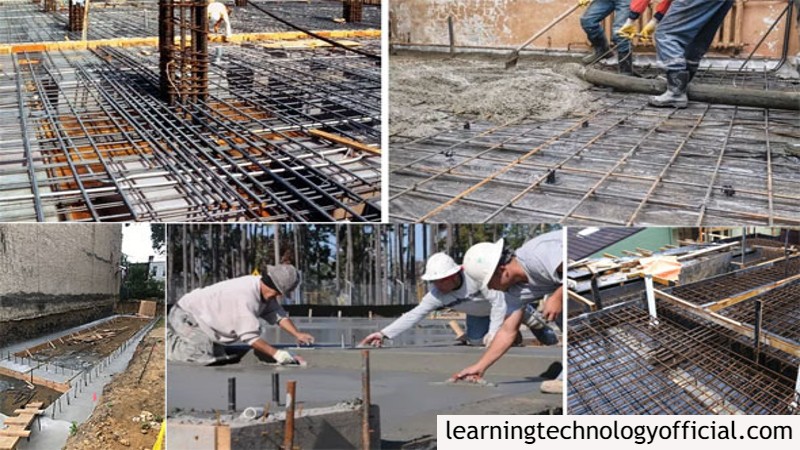
- Reinforcement: Steel reinforcement bars, also known as rebars, are placed within the formwork to enhance the slab’s strength and ability to resist tension. The rebars are positioned according to the design specifications, and any necessary supports or spacers are used to maintain the proper spacing and position of the reinforcement.
- Pouring concrete: Once the formwork and reinforcement are in place, fresh concrete is poured into the formwork. The concrete mixture typically consists of cement, aggregates (such as sand and gravel), water, and sometimes additives or admixtures for improved properties.
- Leveling and finishing: The concrete is leveled and smoothened using tools such as trowels to achieve a flat surface. Additional finishing techniques like trowel texturing or surface treatments may be applied if desired.
- Curing: After the concrete has been placed, it needs to cure properly to gain strength and durability. Curing involves maintaining adequate moisture and temperature conditions for an appropriate period, usually several days, to allow the concrete to harden gradually.
Once the curing process is complete, the formwork can be removed, and the RCC slab is ready for further construction activities or immediate use as a functional surface.
RCC slabs are widely used due to their strength, durability, and versatility. They can be designed to accommodate different load requirements, and their thickness and reinforcement vary based on the intended use and structural considerations.
ALSO READ:
- How to Calculate Loads in Frame Structure Building : Full Guide
- Top 250 Civil Engineering Interview QnA for Practical Site Interview
10 REASONS FOR CRACKS IN RCC SLAB
1. Environment Temperature – The weather in which you are casting your concrete is very vital for your concreting process. If you do not pay attention, then cracks are inevitable in your slab. You always try not to concreting in very hot weather. Try to concrete in the evening time so that the weather will cool down a bit. Due to the provision of concreting in more hot weather, the plastic shrinkage in the slab is developed, due to which the cracks are there, which we have to avoid.
2. Concrete Temperature – Now we will talk about the temperature of concrete, due to which there are chances of getting a lot of cracks. According to ASTM C 1064-4, the temperature of concrete should be in between 27.7 ° C to 35 ° C. If the temperature of concrete is more than 35 ° C, then we should use ice in concrete.
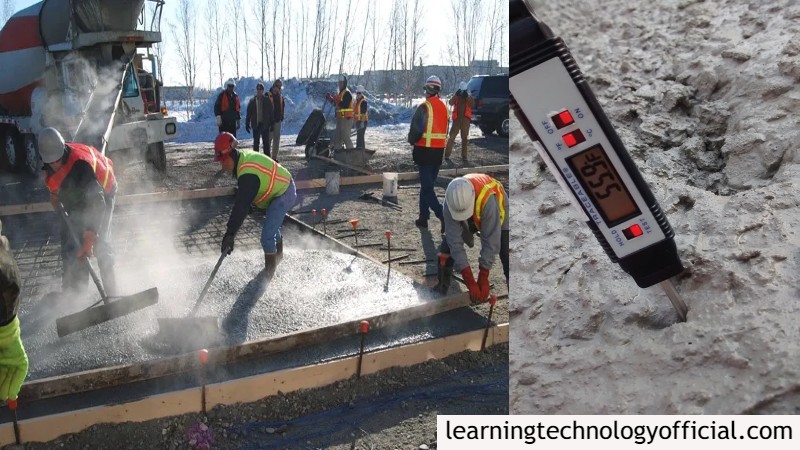
3. Water Cement Ratio – If the water-cement ratio is not maintained properly, its effect is seen in the form of cracks in the slab. Therefore, maintain the water-cement ratio mentioned in the mix design properly. Due to the high water-cement ratio, the concrete gets bleed, in which all the water of the concrete comes on the filter, which is a very vital reason for the cracks.
4. Compaction Frequency – During the casting of concrete we use a vibrator for compaction and for removing the voids. But excessive use of a vibrator is also not good for concrete. With this, the coarse aggregates settle down and fine aggregates start coming up due to which cracks are developed in the slabs. Therefore, keep this in mind while converting.
5. Presence of silt – The presence of silt in fine aggregate also results in hair cracks in concrete. If the silt is present in the sand, it will not be able to bond with cement due to which the concrete will not be set and there will be hair cracks in concrete. So we have to check properly the silt content in sand.
6. Reinforcement Temperature – Crack has also been seen occasionally due to the overheating of the steel bar used in construction works. Therefore, do not concrete casting in too hot weather.
7. Presence of Lubricant on the rebar – The application of grease or shuttering oil or any kind of Lubricant on the rebar can prove fatal for concrete. There will never be the bonding of concrete and bars due to which we can get cracks.
8. The difference in Slump Test Value – When we do casting on-site, we take a slump test by taking concrete from different lots. So the value of these different lot’s slump tests should not have much difference in the character, because of this also the cracks have been seen in the slab.
9. Types of Cement – You all know cement is of many types. Choosing the right cement in construction work can save you from getting cracks. You should choose cement keeping in mind the weather and work type. In the slab, if you use cement whose heat of hydration is very high, then the chances of cracks in the slab will become higher.
10. Overheating of shuttering material – Cracks can also be seen occasionally due to the heating of the shuttering material especially for Steel shuttering material. But the effect is very minor.
In this way, keeping in mind all these things, we can save the cracks from coming in the slabs.
REFERENCE VIDEO : RCC SLAB CRACKS REASONS AND SOLUTION
If You Want Detailed Knowledge Then Watch My Video On YouTube Channel: Learning Civil Technology. I Am Telling This Because Many Important Points I Have Covered During Making Of Video, So If You Want To Know In Detail Then Watch My Video On YouTube Which is Given Below.
You can also follow me on Instagram, Telegram and Facebook page. Because many small things, which are very important from interview point of view, it is not possible to put here, I put all that on Instagram, Telegram and Facebook page. You can take it from there. You will find the links of all social media below.
INSTAGRAM | TELEGRAM | FACEBOOK PAGE
SHARE THIS POST, IF YOU LIKE IT !! THANKS
How to measure concrete temperature between 27.7 to 35 degrees