To maintain the longevity and stability of structures, a variety of methods and tools are used in the construction business. The cement grouting machine is one such piece of crucial equipment. This page attempts to give a thorough overview of cement grouting machines, including information on their kinds, operating theories, applications, benefits, selection criteria, safety considerations, grouting best practices, troubleshooting methods, maintenance recommendations, and upcoming developments.
Contents
- 1 What is a Cement Grouting Machine?
- 2 Types of Cement Grouting Machines
- 3 Working Principle of Cement Grouting Machines
- 4 Applications of Cement Grouting Machines
- 5 Advantages of Using Cement Grouting Machines
- 6 Factors to Consider When Choosing a Cement Grouting Machine
- 7 Safety Precautions for Operating Cement Grouting Machines
- 8 Tips for Effective Grouting with Cement Grouting Machines
- 9 Common Challenges and Troubleshooting Techniques during Cement Grouting with machines
- 10 Maintenance and Care of Cement Grouting Machines
- 11 Future Trends in Cement Grouting Machines
- 12 Cost of Cement Grouting Machines
- 13 Conclusion
- 14 Frequently Asked Questions – FAQs
What is a Cement Grouting Machine?
A specialized tool called a cement grouting machine is used to inject grout ingredients into cracks, cavities, and concrete structures. The targeted regions are strengthened, repaired, or waterproofed as a result. These tools are frequently employed in mining operations, tunneling projects, and building projects.
A device used in construction and civil engineering projects for injecting or pumping cementitious grout into various buildings is a cement grouting machine, often known as a grout pump or injection pump. Filling spaces or holes in soil, rock, or concrete with a fluid combination known as grout is the process of grouting.
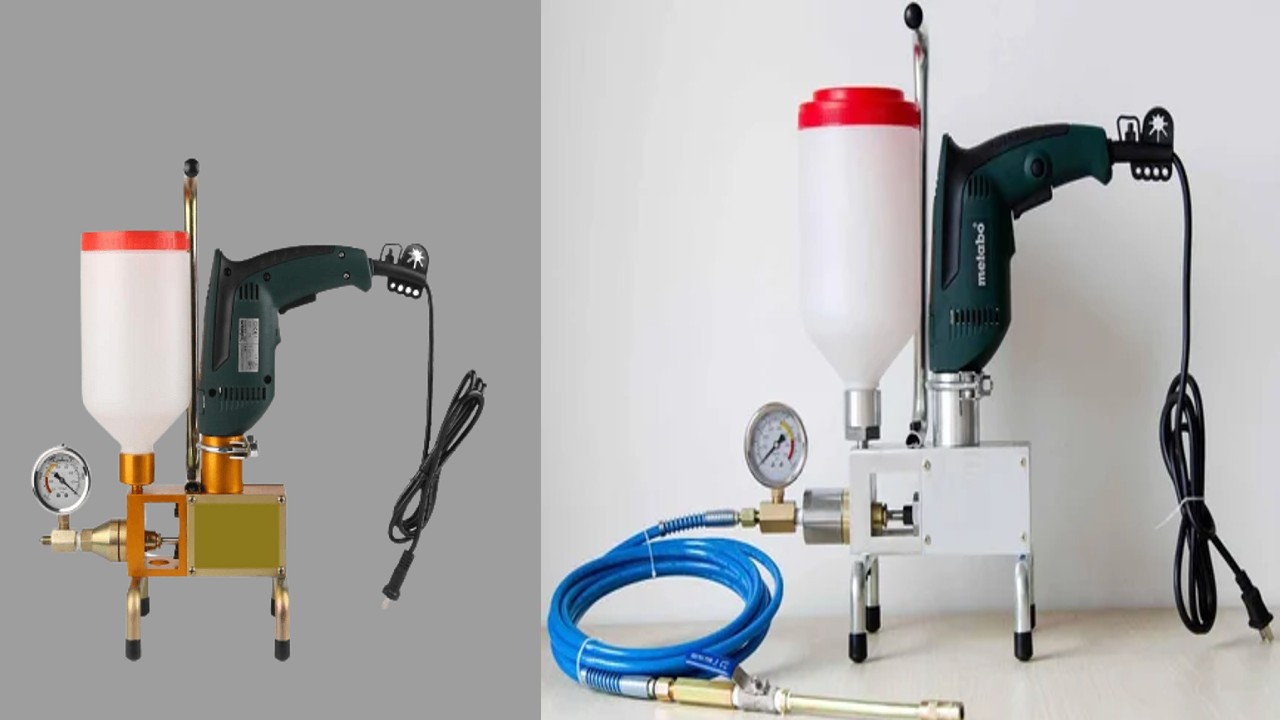
Types of Cement Grouting Machines
Cement grouting machines come in a variety of designs, each with particular benefits and characteristics. The primary kinds consist of:
Piston Type Grouting Machine: The grout is pumped by a reciprocating piston in this kind of grouting equipment. By oscillating within a cylinder, the piston provides pressure that forces the grout mixture to flow via valves and outlets. High pressure and the capacity to work with viscous grouts are two characteristics of piston grouting machines. They are frequently employed for tasks including foundation restoration, void filling, and soil stabilization.
Screw Type Grouting Machine: A screw pump mechanism is used by screw grouting machines to pump the grout. The grout is propelled forward by the screw, sometimes referred to as an auger, which rotates inside a cylindrical housing. This kind of equipment is especially well suited for abrasive grout mixes that incorporate aggregates or particles. In mining, tunneling, and initiatives aimed at improving the soil, screw grouting machines are frequently employed.
Plunger Type Grouting Machine: Plunger or ram mechanisms are used in plunger grouting machines to create pressure and pump grout. The grout is forced through the system by a plunger that oscillates back and forth inside a cylinder. These devices can work with both chemical and cementitious grouts and are appropriate for medium to high-pressure grouting applications. Machines for plunging grout are often employed in many types of building projects.
Peristaltic Type Grouting Machine: The spinning roller mechanism in peristaltic grouting machines compresses a flexible tube to pump the grout. The grout is compressed and propelled ahead as the roller travels along the tube. Since it doesn’t damage the grout, this kind of equipment is appropriate for fragile or shear-sensitive materials. In applications like injection grouting, where precise placement is essential, peristaltic grouting machines are frequently employed.
Injection Type Grouting Machine: Machines for injecting grout into fractures, joints, or confined places are known as injection grouting machines. These devices frequently contain a small nozzle or needle that enables precise and precise grout placement. They are frequently employed in projects involving structural reinforcement, waterproofing, and concrete crack repair. Depending on the particular machine design, injection grouting machines may use a variety of pumping methods, including piston, plunger, or peristaltic.
Jet Grouting Machine: To mix and stabilize the soil, jet grouting machines spray grout at high velocity. High pressure grout is pushed through a nozzle to solidify the dirt into a column. In difficult ground conditions, jet grouting is frequently utilized for foundation support, ground consolidation, and soil enhancement. Depending on the particular jet grouting technology used, jet grouting machines come in a variety of designs, including single-fluid and double-fluid systems.
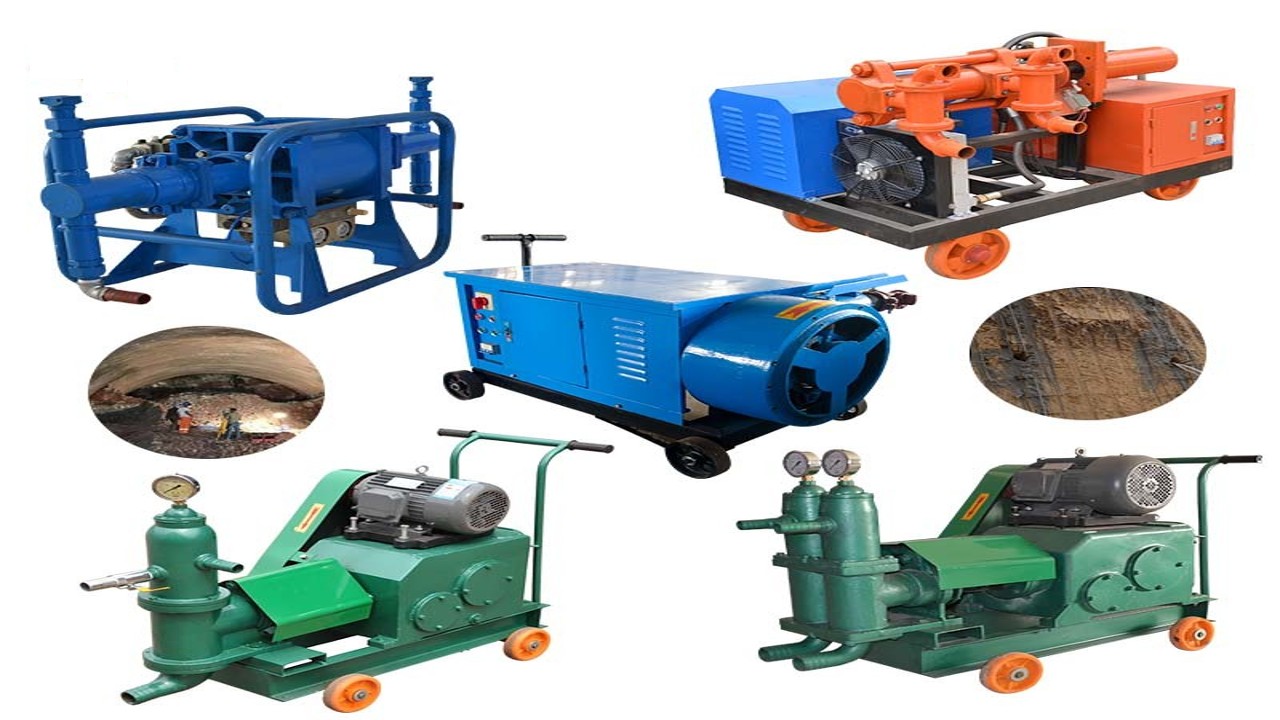
These are the primary varieties of cement grouting machines that are available, each with specific benefits and adaptability for certain tasks. The project requirements, grout characteristics, required pressure and flow rate, and the application’s specifics all play a role in choosing the right kind.
Also Read: Epoxy Grout vs. Cement Grout vs. Cement Mortar: Decoding the Variations
Working Principle of Cement Grouting Machines
In order to create a homogenous slurry, cement grouting machines combine the grout ingredient with water or other additives. Through a nozzle or injection port, this mixture is subsequently pushed under pressure into the desired location. The grout fills in the gaps, crevices, or spaces, strengthening the surrounding material’s integrity and supplying structural support.
Source: Acme Equipment SG
Applications of Cement Grouting Machines
Machines for cement grouting have several uses in civil engineering and building projects. Here are some specific uses for cement grouting equipment:
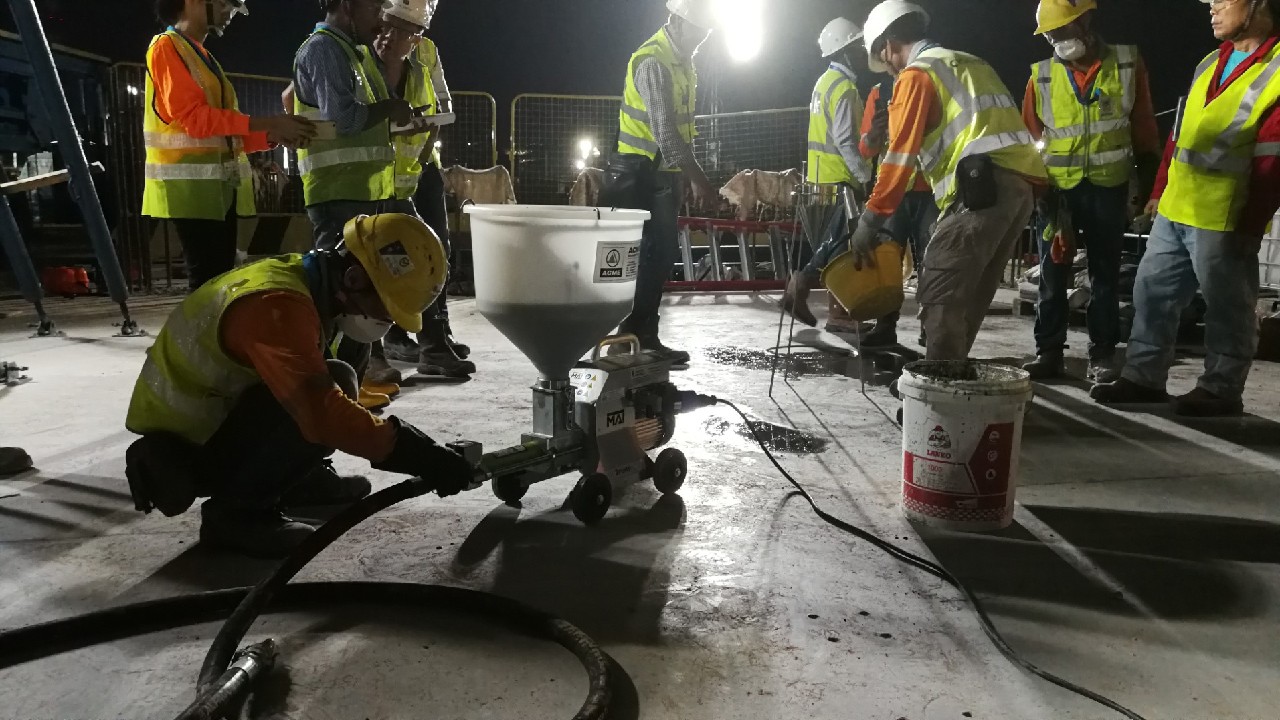
Soil Stabilization: To increase the strength and stability of the earth, cement grouting machines are used for soil stabilization. A solid mass that improves load-bearing capacity is created when grout is injected into weak or loose soil forms. This method is frequently used in foundation building, railroad and highway embankments, and slope stabilization projects.
Foundation Repair: In foundation repair, grouting machines are used to solve problems including settlement, cracks, and voids. In order to fill voids and stabilize the soil, grout is injected into the foundation. This improves the foundation’s integrity by preventing additional settling. The structural integrity of structures and infrastructure depends on this use.
Concrete Crack Repair: Machines for cement grouting are essential for patching cracks in concrete buildings. Grout is injected into the fractures to seal them off and stop future degradation and moisture intrusion. Maintaining the structural integrity of bridges, dams, tunnels, and other concrete structures requires this application.
Tunneling and Mining: Machines for grouting are frequently employed in mining and tunneling projects. To support the tunnels, restrict water entry, and increase overall safety, grout is injected into the nearby rock formations. Grouting improves the stability of tunnels and underground excavations by helping to consolidate loose earth, increase rock mass, and reduce ground movement.
Void Filling: In buildings like abandoned mines, caverns beneath the ground, and sinkholes, voids are filled with cement using cement grouting equipment. These holes are filled with grout, which also supports the surrounding regions by effectively filling them. Potential collapses, subsidence, and ground instability are avoided via void filling.
Waterproofing: Especially in basements, subterranean constructions, and concrete water-retaining structures, grouting machines are used for waterproofing purposes. A waterproof barrier is created by injecting grout into the seams, fissures, or concrete surfaces, stopping water infiltration. This preserves the buildings’ lifespan and protects them from water damage.
Dam Rehabilitation: Machines for cement grouting are necessary for initiatives aimed at restoring dams. To improve the integrity of the dam and stop water leakage, grout is injected into the dam’s construction to plug holes, cracks, and fissures. The stability and efficiency of dams are maintained with the aid of this application.
Structural Strengthening: Grouting machines are used for structural strengthening tasks including boosting an existing structure’s load-bearing capacity or fixing broken components. To improve the structural performance, stability, and longevity of buildings, bridges, and other infrastructure, grout is injected into the appropriate regions.
These uses highlight the adaptability and value of cement grouting equipment in various construction and maintenance tasks. The equipment makes efficient and accurate grout injection possible, enhancing the general stability, lifespan, and safety of structures.
Also Read: Easy Cement Calculation: How to Calculate 1 Bag (50kg) Cement Volume in CUM CFT Litre?
Advantages of Using Cement Grouting Machines
There are various benefits to using cement grouting machines in construction and civil engineering projects. The following are specific benefits of employing cement grouting machines:
Efficient Grout Injection: The injection of grout into crevices, fissures, or gaps may be done very effectively with cement grouting machines. The equipment is made to move enormous amounts of grout at regulated pressures and flow rates. Faster grouting operations shorten project timelines and boost production because to this efficiency.
Precise Placement: Cement grouting machines make it possible to put grout precisely where it is needed. The machines come with nozzles, needles, or accessories that provide users precise control over the grout flow. This accuracy is essential in applications like fixing concrete cracks or injecting grout, where the grout needs to get to particular places to adequately strengthen or seal the structure.
Increased Bonding and Strength: Strong bonds are made between the surrounding materials and grout that has been injected utilizing grouting equipment. The machines’ high pressure guarantees that the grout is properly compacted, reducing cavities and improving contact with the substrate. This improves the overall stability and longevity of the treated region by boosting bonding and increasing structural strength.
Versatility: In terms of grout formulations and application methods, cement grouting machines are flexible. Grouts of all kinds, including cementitious, chemical, and speciality grouts, may be handled by the machines. Additionally, they may support different application techniques as pressure grouting, jet grouting, or permeation grouting. This adaptability enables customized solutions to satisfy the unique needs of various projects.
Control over Flow and Pressure: Machines for grouting offer exact control over the grout’s flow rate and pressure. In order to ensure optimal grout penetration and distribution, skilled operators can change the parameters to correspond with the project specifications. This control aids in preventing over- or under-grouting and helps produce uniform grouting results, leading to a more dependable and consistent output.
Cost-Effectiveness: Construction projects may save money by using cement grouting equipment. Reduced labor expenses are the result of the effective grout injection procedure, which minimizes labor time and effort. Additionally, the ability to adjust the grout’s flow and pressure enables effective use of the grout mixture and reduces material waste.
Enhanced Structural Integrity: Cement grouting machines improve the structural integrity of structures, infrastructure, and geological formations by filling gaps, stabilizing soil, fixing fractures, or fortifying structures. The problematic regions are strengthened by the grout that the machines inject, reducing the likelihood of settlement, movement, or additional degradation. In consequence, this increases the buildings’ longevity and lessens the need for future expensive repairs.
These benefits demonstrate how crucial cement grouting machines are for completing grouting operations that are effective, accurate, and dependable. The equipment helps ensure safe and long-lasting constructions by enhancing the general quality, strength, and durability of construction projects.
Also Read: Wall Putty: Types, Process, Importance, Benefits, Application, Costing Comprehensive Guide
Factors to Consider When Choosing a Cement Grouting Machine
Several aspects should be taken into account when selecting a cement grouting machine for a construction or civil engineering project. These elements consist of:
Project Requirements: Examine the project’s precise needs, including the amount of grout to be injected, the necessary pressure and flow rate, and the kind of grout mixture to be utilized. To make sure the grouting machine can efficiently satisfy the project’s demands, take into account its size, capacity, and capabilities.
Type of Grout: Different grouting machines are made to work with particular kinds of grout, such speciality, chemical, or cementitious grouts. Think about whether the machine will work with the particular grout mixture needed for the project. Make that the grout’s viscosity, particle size, and other characteristics are compatible with the pumping mechanism and other parts of the machine.
Application Method: Choose the application technique—such as permeation grouting, pressure grouting, injection grouting, or jet grouting—that best meets the project’s needs. Choose a grouting machine with the attachments or accessories required for precise and controlled grout placement, as well as support for the preferred application technique.
Pumping Capacity: To make sure the machine can handle the needs of the project, take into account the needed grout volume and pumping rate.
Pressure Rating: Choose a machine that can produce the appropriate pressure after determining the maximum pressure needed for the grouting application.
Pumping Mechanism: Pumping mechanisms used by various types of grouting machines include piston, screw, plunger, and peristaltic pumps. Every mechanism has benefits and is suitable for particular applications. To select the most suitable pumping mechanism for the project, take into account elements like the needed pressure, flow rate, viscosity of the grout, and the presence of abrasives or particles.
Mobility and Accessibility: Analyze the project site’s needs for accessibility and mobility. Ascertain if a truck-mounted, skid-mounted, or portable grouting machine is required. To make sure the chosen equipment can be deployed and moved about successfully on-site, take into account aspects including the site’s characteristics, space restrictions, and the necessity for easy transportation.
Reliability and Durability: Choose a grouting machine that has a reputation for dependability, toughness, and performance. Take into account the construction’s quality, the materials employed, and the manufacturer’s or supplier’s standing. During the grouting process, a dependable equipment with durable construction will ensure efficient operation, longevity, and little downtime.
Operator Skill Level: Take into account the degree of operator expertise and experience needed to run the grouting equipment successfully. It’s possible that certain machines have more intricate controls or need specialist training. To guarantee safe and effective operation, select a machine that is compatible with the operators’ current level of ability.
Maintenance and Service: Evaluate the grouting machine’s maintenance and service support options. Take into account elements like the accessibility of replacement parts, technical assistance, and the manufacturer’s or supplier’s track record for post-purchase support. A machine with dependable maintenance and support solutions will save downtime and guarantee consistent performance throughout the project.
By carefully taking into account these variables, you may choose the cement grouting machine that best fits your needs, increases productivity, and produces grouting results of the highest caliber.
Also Read: MS Angle Weight Chart PDF: Calculate MS Angle Weight for On-Site Billing in 3 Steps
Safety Precautions for Operating Cement Grouting Machines
To avoid accidents and protect the safety of operators and personnel participating in building projects, cement grouting machines must be operated safely. When using cement grouting equipment, keep the following safety measures in mind:
Read and Understand the Manual: Read the manufacturer’s manual and the grouting machine’s operating instructions thoroughly. Recognize the features, settings, and safety instructions that the manufacturer has supplied for the equipment.
Wear Personal Protective Equipment (PPE): Always put on the proper personal protection gear, such as safety boots, gloves, hard helmets, and safety glasses. PPE aids in preventing risks including flying objects, chemicals, and unintentional spills.
Training and Competence: Make sure that everybody using the grouting machine has gotten the appropriate training and is proficient in using it. Training should address grout material handling best practices, safety precautions, and emergency measures.
Machine Inspection: Before each usage, give the grouting machine a complete examination. Look for any indications of leaks, loose pieces, or damage. Make sure that all barriers, coverings, and safety equipment are in place and working correctly.
Secure the Work Area: To prevent unwanted entry, provide a secure work space surrounding the grouting equipment. Set up barriers or warning signs to block off areas clearly marked off to keep unauthorized people and bystanders away from the machine while it is in use.
Ventilation: Make sure the workspace has enough ventilation, especially if you’re working inside or in a small area. The danger of exposure to gases, dust, or other airborne pollutants produced during grouting activities is reduced with the aid of proper ventilation.
Grout Mixture Handling: Use the correct techniques while handling and mixing grout ingredients. For measuring and combining the grout, use the proper equipment and containers. When handling chemicals or additives, keep skin and eyes away from them and make sure there is adequate ventilation.
Pressure and Flow Control: Use caution when altering the grouting machine’s pressure and flow parameters. Start with a lesser pressure and then raise it as necessary. Avoid using too much pressure, which might damage your equipment or result in an unintentional high-velocity grout spray.
Emergency Stop and Shutdown: Learn how to use the grouting machine’s emergency stop and shutdown mechanisms. In the event that an instant shutdown is necessary, be aware of where and how to use the emergency buttons or switches.
Cleaning and Maintenance: Follow the manufacturer’s directions while cleaning and maintaining the grouting machine on a regular basis. Cleaning properly helps avoid accumulation or blockage that can cause equipment failures. Before performing maintenance or repairs, disconnect the power supply and observe proper lockout/tagout procedures.
Communication and Coordination: During grouting operations, keep lines of communication open with other on-site employees. In order to maintain efficient cooperation and warn others of potential dangers, use hand signals, radios, or other appropriate techniques.
Utilizing cement grouting equipment safely helps reduce the possibility of mishaps, injuries, or property damage. Always put safety first, and follow any applicable rules and policies that are relevant to the situation and the needs of the project.
Also Read: Concrete Mixer Machine: Versatile Tool for Construction Projects 2023
Tips for Effective Grouting with Cement Grouting Machines
The following advice should be taken into account to enable efficient grouting with cement grouting machines:
Proper Mix Design: Pay close attention to the grout mixture’s mix design. To get the appropriate consistency and qualities of the grout, use the recommended ratios and quantities of cement, water, and any additives. To avoid any lumps or clumps, be sure to thoroughly combine the ingredients.
Pre-wetting: Before injecting the grout, pre-wet the substrate or surfaces that will be grouted. This promotes better bonding and reduces shrinkage by preventing the water from the grout mixture from being absorbed.
Surface Preparation: Cleaning the surfaces completely will prepare them for grouting. Eliminate any loose materials, impurities, or pollutants that could prevent the grout’s appropriate adherence and flow. To strengthen the bond between the grout and the substrate, roughen smooth surfaces or, if necessary, use bonding chemicals.
Flow Rate and Pressure Control: During injection, keep the grout’s flow and pressure under control. To ensure a consistent and uniform application, start with lower flow rates and progressively increase as necessary. To avoid over- or under-grouting, adjust the pressure based on the needs of the project and the properties of the substrate.
Injection Pattern: Choose the right injection pattern for the particular project. Think about things like the grout’s qualities as well as the size and shape of the holes or fissures. To guarantee comprehensive coverage and grout penetration into the desired locations, adopt a methodical technique.
Venting and Bleeding: After grout injection, give yourself enough time for venting and bleeding. This makes sure that any air pockets or trapped air inside the grout are eliminated, which might impact the grout’s functionality and lead to weak places. A firm and even grout mass is easier to create with proper venting and bleeding.
Monitoring and Quality Control: Keep an eye on the grouting procedure and examine the injected grout. To maintain uniformity and efficiency, keep track of the flow rate, pressure, and other factors. Conduct routine visual examinations of the grouted areas to look for evidence of leakage or abnormalities, correct fill, and the absence of voids.
Post-Grouting Treatment: Depending on the needs of the project, implement the advised post-grouting procedures, such as curing or sealing. The grout can acquire the appropriate strength and durability with proper curing. In order to shield the grouted areas from moisture infiltration or other environmental variables, use sealants or coatings as appropriate.
Clean and Maintain the Equipment: After grouting is finished, carefully clean the grouting machine to get rid of any leftover grout or dirt. The equipment’s lifetime is ensured by regular cleaning and repair, which also helps to avoid contamination or obstructions during subsequent grouting operations.
These recommendations will help you maximize the bonding, stability, and longevity of the treated regions while using grouting machines to apply cement. The project-specific best practices and standards should be followed for good grouting results.
Common Challenges and Troubleshooting Techniques during Cement Grouting with machines
There might be a number of difficulties while grouting cement using machinery. The following are some typical issues and their resolution methods:
1. Insufficient Grout Penetration
If the grout does not penetrate the required locations sufficiently, cavities or fractures may not be completely filled. High grout viscosity, insufficient pressure, or injection system clogs are a few potential causes.
Troubleshooting Techniques:
- To get the necessary viscosity for improved flow and penetration, modify the grout mix design.
- Gradually raise the pressure while making sure it stays within the acceptable range for the given application.
- Examine the grout lines, nozzles, and fittings for any obstructions and remove them if required.
- To encourage grout penetration into difficult places, use the right injection methods, such as pulsing or intermittent injections.
2. Grout Leakage or Seepage
Unintentional grout seepage or leaking during injection might result in ineffective grouting and possible structural problems. Cracks in the substrate, poor sealing, or too much grout pressure can all result in leaks.
Troubleshooting Techniques:
- Look for any cavities or fissures in the substrate that might be letting grout escape. Before grouting any such holes, seal them.
- To avoid grout leaking, make sure the injection sites or joints are properly sealed.
- If the grout pressure is too high or is resulting in too much seepage, lower it.
- To reduce leakage, adjust the injection procedure to manage the flow rate and give enough time for cure.
3. Grout Segregation or Settling
When solid grout particles sink to the bottom, segregation happens, producing an uneven mixture. The strength and characteristics of the grout may change as a result.
Troubleshooting Techniques:
- Before injection, make sure the grout mixture has been well mixed to produce a consistent consistency.
- To increase the stability and suspension of solid particles, if suggested, use the proper admixtures or additions.
- To avoid settling, don’t wait too long between mixing and injection.
- Depending on the application, think about utilizing thixotropic or self-leveling grouts to reduce segregation.
4. Equipment Malfunctions or Blockages
The grouting procedure may be hampered and the grout flow may be interfered with by problems with the grouting equipment, such as pump failures or obstructions in the injection system.
Troubleshooting Techniques:
- Follow the manufacturer’s suggested maintenance methods while inspecting and maintaining the grouting machine on a regular basis.
- After every usage, properly clean the machine to remove any grout accumulation or obstructions.
- Verify that the valves, fittings, and pressure gauges are operating properly, and fix or replace any broken parts.
- Using the proper equipment or cleaning solutions, remove any obstructions from the grout nozzles or lines.
5. Grout Shrinkage or Cracking
During the curing phase, grout shrinkage or cracking might happen, threatening the integrity of the grouted regions. These problems may be caused by elements like poor mix design, insufficient curing, or excessive drying.
Troubleshooting Techniques:
- Make certain the grout mix design is suitable for the particular application, taking into account elements like the water-to-cement ratio and additives.
- Reduce shrinkage and encourage adequate hydration by adhering to suitable curing processes, such as wet curing or employing curing chemicals.
- Avoid accelerated drying times and high heat, which can cause early cracking. Apply safety precautions include covering the grouted areas with plastic sheeting or damp burlap.
Consult with seasoned professionals or grouting specialists in the event of enduring difficulties or complicated problems so they can offer professional advice and direction to handle any concerns unique to cement grouting.
Maintenance and Care of Cement Grouting Machines
The lifespan, dependability, and optimum performance of cement grouting machines depend on proper maintenance and care. Here are some crucial procedures for caring for and maintaining cement grouting equipment:
Regular Cleaning: After every usage, properly clean the grouting machine. Clean out the hopper, lines, valves, and fittings of the machine of any leftover grout, dirt, or silt. Use the proper cleaning supplies and equipment to make sure that there is no grout accumulation or obstruction on any of the components.
Lubrication: For grouting machine lubrication, go by the manufacturer’s instructions. To reduce friction and wear, regularly lubricate moving components like pistons, plungers, or screw mechanisms. Use lubricants that are compatible with the parts of the machine as advised.
Inspection and Replacement of Parts: Make regular checks of the grouting machine to find any worn, damaged, or broken parts. Examine the hoses, seals, gaskets, and fittings for leaks, cracks, or wear. To avoid equipment failure or safety risks, rapidly replace any defective or worn-out components.
Calibration and Adjustment: To maintain precision and consistency, calibrate and modify the grouting machine’s pressure and flow parameters on a regular basis. To maintain peak performance, use the proper calibration tools and adhere to the manufacturer’s instructions. To guarantee that pressure gauges offer correct readings, check and calibrate them often.
Electrical and Power System Maintenance: Check the electrical connections and components to make sure they are in excellent working order if the grouting machine is driven by an electric motor. Check cables, switches, and control panels often for any indications of damage or faulty connections. Follow the manufacturer’s recommendations for routine oil changes, filter replacements, and fuel system inspections if the equipment has a diesel engine.
Storage and Protection: When not in use, keep the grouting machine in a tidy, dry location. Avoid exposing it to severe weather, direct sunshine, or extremely high or low temperatures, which might harm the equipment. To stop dust, dirt, or moisture accumulation, if required, cover the machine with a tarp or other protective covering.
Operator Training and Safety: Make that operators are appropriately instructed in the upkeep, safety, and operation of the grouting equipment. By following pertinent safety standards and recommendations, you may foster a culture of safety. Give operators the required PPE and make sure they utilize it correctly while grouting activities are underway.
Manufacturer’s Recommendations: Observe the grouting machine’s manufacturer’s recommended maintenance schedule. For detailed maintenance instructions, suggested service intervals, and any other recommendations or safety measures particular to the equipment, see the machine’s user manual or get in touch with the manufacturer.
Cement grouting machines benefit from routine maintenance since it increases their lifespan and maintains their effective and safe functioning. You may minimize downtime, lower the chance of equipment failure, and improve the grouting machine’s performance and dependability by putting these maintenance and care procedures in place.
Future Trends in Cement Grouting Machines
Technology developments and new trends in the construction sector are driving the continued development of cement grouting machines. Here are some prospective developments in cement grouting equipment for the future:
Automation and Robotics: We may anticipate seeing more automation in cement grouting equipment as automation and robotics technology develop. For operations like grout mixing, flow control, adjusting injection patterns, and monitoring, automated systems can be created. Robotics may be used to place grout precisely and consistently, increasing productivity and requiring less manual work overall.
Smart and IoT Integration: Cement grouting machines’ capabilities and usefulness can be improved by integrating smart technologies and the Internet of Things (IoT). Real-time data on grout flow, pressure, temperature, and other factors may be gathered using smart sensors and monitoring systems. Remote transmission and analysis of this data enables operators to improve grouting procedures and make wise judgments.
Data Analytics and Predictive Maintenance: Data analytics may be used to track and evaluate the performance of cement grouting equipment with the incorporation of IoT technology. In order to prevent problems from occurring in the first place and save downtime, proactive maintenance may be carried out using machine learning algorithms and predictive maintenance approaches. By using this method, equipment performance may be improved and grouting machine lifespans can be increased.
Improved Efficiency and Precision: Future cement grouting machines will probably emphasize increasing productivity and accuracy in grouting operations. It is possible to distribute grout more precisely and controllably, resulting in less waste and optimal coverage, with the help of improvements in pumping mechanisms, flow control systems, and injection procedures. Faster grout mixing and injection rates may be offered by higher efficiency devices, boosting productivity on building sites.
Eco-friendly Grout Materials: The development of environmentally friendly grout materials may be influenced by the increasing emphasis on sustainability in building. These materials, including bio-based grouts or more ecologically friendly cement substitutes, can be accommodated by cement grouting machines. These materials seek to lessen carbon emissions, increase sustainability, and improve the grouting process’s long-term environmental effect.
Remote Operation and Telematics: Operators may be able to command and keep an eye on cement grouting machines from one central place thanks to developments in remote operation and telematics technology. This function, which enables remote diagnostics, troubleshooting, and grouting process optimization, might be especially useful for large-scale projects or remote sites. The ability to operate remotely can improve cooperation, increase safety, and expedite operations.
Integration with Building Information Modeling (BIM): Better project planning, coordination, and information sharing may be made possible with the integration of cement grouting machines with Building Information Modeling (BIM). By enabling virtual simulations and collision detection to improve grout placement and reduce conflicts with other building elements, BIM models may offer useful insights into the grouting process.
These upcoming developments in cement grouting equipment show how the sector is always working to increase productivity, precision, sustainability, and connection. Adopting these innovations can result in grouting operations that are more efficient and long-lasting, improving the general quality and durability of building projects.
Cost of Cement Grouting Machines
The price of cement grouting machines can vary based on a number of variables, including the machine’s type and size, brand, features, and market circumstances. The following price ranges are typical for cement grouting equipment:
Small to Mid-Range Machines: Small to medium-sized cement grouting machines can cost anywhere from $1,000 and $10,000, making them ideal for smaller-scale projects or niche applications. These devices are often more portable and may have simpler features and lower pumping capacity.
Mid-Range to High-End Machines: Mid-range to high-end cement grouting machines can cost anywhere from $10,000 and $50,000 or more and include cutting-edge features, greater pumping capacity, and increased durability. These devices are frequently more resilient, adaptable, and ideal for a variety of grouting applications.
Specialized or High-Capacity Machines: Price ranges can be greater for specialized or large-capacity cement grouting machines equipment made for difficult or complicated applications, such mining or tunneling. These devices could have specialized functions, robust parts, and sophisticated pumping mechanisms. Such robots can cost anything between $50,000 and several hundred thousand dollars.
It’s vital to keep in mind that these price ranges are only estimates and may change depending on the location, source, manufacturer, extra accessories or attachments, and any customisation or optional features required.
It’s important to consider the cost of a cement grouting machine over the long term, taking into account aspects like durability, reliability, performance, maintenance needs, and any after-sales support offered by the manufacturer or supplier, in addition to the initial purchase price.
Before making a purchase, it is advised to speak with a number of suppliers or manufacturers, evaluate costs, specs, and reviews, and take into account the particular needs of your project.
Conclusion
In order to reinforce and repair concrete structures, increase construction efficiency, and ensure the durability of structures and infrastructure, cement grouting machines are essential. Construction professionals may make wise choices and obtain excellent grouting results by understanding the many kinds, operating principles, applications, selection criteria, and maintenance methods related with these machines.
Frequently Asked Questions – FAQs
What is the purpose of a cement grouting machine?
To reinforce, repair, or waterproof buildings, voids, or fractures, grout ingredients are injected using a cement grouting machine.
How does a cement grouting machine work?
In order to fill gaps or fractures, cement grouting machines combine grout components with water, pump the mixture under pressure, and inject it into the desired location.
What are the key factors to consider when choosing a cement grouting machine?
Pumping capacity, pressure rating, grout mixing and injection system, mobility, and maintenance needs are all significant variables to take into account.
Are cement grouting machines safe to use?
Cement grouting machines are safe to use when used in accordance with the recommended safety measures. Both appropriate training and personal safety equipment are necessary.
How can I maintain a cement grouting machine effectively?
To efficiently maintain a cement grouting machine, regular cleaning, lubrication, inspections, and quick repairs or replacements of broken parts are essential.