The correct materials must be used for building and remodelling projects in order to get the intended outcomes. Grouts and mortars are essential in the world of tiling and flooring. Epoxy grout, cement grout, and cement mortar are some of the choices that are frequently employed. Making educated decisions requires an understanding of the variations between different materials. We shall examine the features, benefits, and uses of epoxy grout, cement grout, and cement mortar in this post, illuminating their distinct qualities.
Contents
Epoxy Grout
Definition and Composition
A specialised form of Grout noted for its extraordinary durability and resistance to stains and chemicals is epoxy grout. Epoxy resins, a filler powder, and a hardener make up its components. Epoxy resins serve as the grout’s primary binders and give it a sturdy, adaptable structure. The filler powder, which is commonly made of finely powdered minerals, aids in giving the grout mixture more volume and improving its overall consistency.
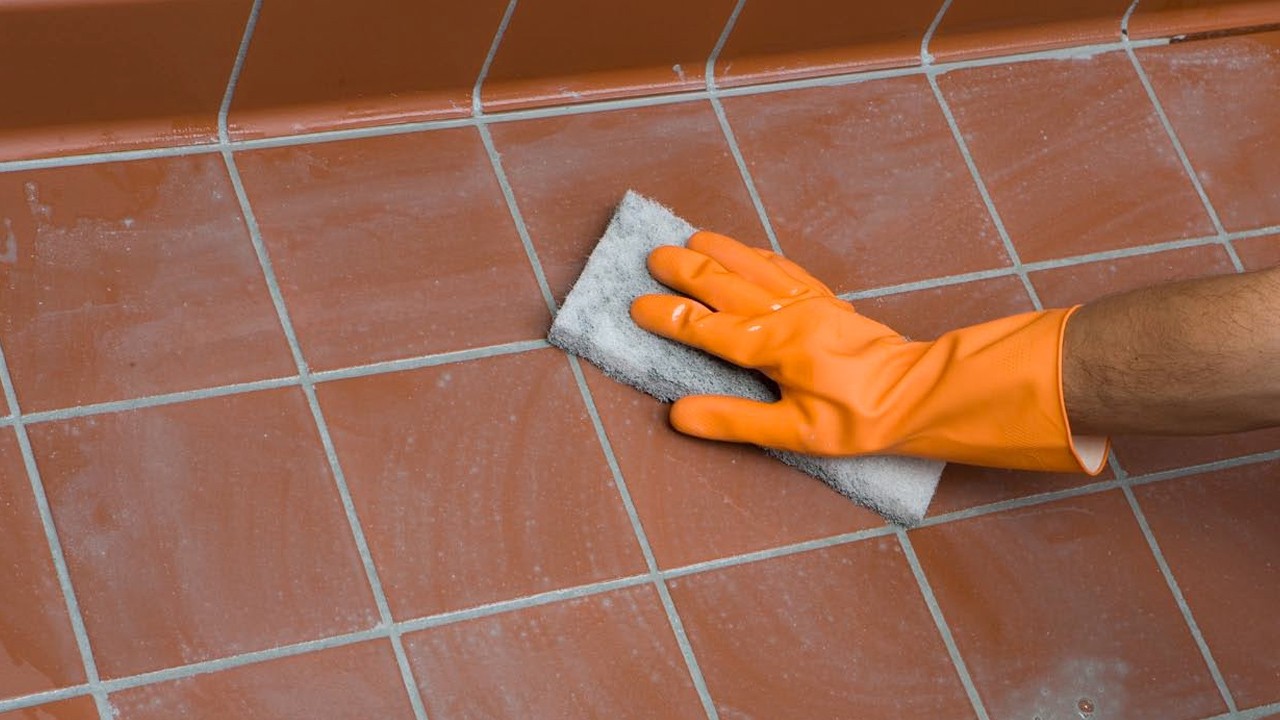
The hardener acts as a catalyst to start the chemical reaction between the filler and epoxy resins, which eventually causes the grout to harden and solidify. Epoxy grout’s non-porous qualities, which make it highly impervious to water infiltration and discoloration, are a result of its distinctive composition. Epoxy grout is furthermore offered in a range of colours, enabling greater design versatility and customisation.
Characteristics and Advantages
Epoxy grout is a popular option for many applications because it has a number of standout qualities and benefits. The following are some essential qualities and advantages of epoxy grout:
Exceptional Durability: Epoxy grout is extremely robust and can sustain large loads and busy locations without breaking or losing its quality. It offers enduring performance and over time keeps its structural integrity.
Non-Porous and Stain-Resistant: Epoxy grout’s lack of pores is one of its many noteworthy benefits. It creates a solid, impermeable barrier that keeps pollutants like water, dirt, and other liquids out of the grout lines. It also has a strong stain resistance due to this quality, making maintenance and cleaning simpler.
Chemical Resistance: Excellent resistance to a variety of substances, such as acids, alkalis, and cleaning solutions, may be shown in epoxy grout. It is appropriate for areas including commercial kitchens, labs, and industrial settings where exposure to chemicals is common.
Mold and Mildew Resistance: Epoxy grout has a very low absorption rate, making it very resistant to the formation of mould and mildew. This is especially helpful for maintaining a clean and hygienic atmosphere in places with high moisture levels, such restrooms and showers.
Design Flexibility: Epoxy grout may be customised and comes in a variety of colours, providing for creative design options. By contrasting or matching the grout colours with the tiles, it provides the potential to improve the aesthetic appeal of tiled surfaces, producing a variety of aesthetically pleasing results.
Ease of Maintenance: Epoxy grout requires less maintenance because of its non-porous and stain-resistant characteristics. The grout lines may often be kept looking clean and new with routine cleaning using mild detergents and non-abrasive instruments.
Enhanced Bonding and Adhesion: A solid and sturdy installation is guaranteed by the strong connection that epoxy grout creates with tile surfaces. This trait helps the tiled structure’s overall durability and strength.
It’s crucial to remember that while epoxy grout has many benefits, it also needs to be handled carefully and applied correctly. For the greatest results while using epoxy grout, it is crucial to adhere to manufacturer specifications and suggestions.
Also Read: Calculating Cement, Sand, and Aggregate Quantity in Concrete: A Step-by-Step Guide
Applications
Due of its outstanding qualities, epoxy grout has many uses in a variety of locations and sectors. Here are some typical applications for epoxy grout:
Commercial and Industrial Flooring: In commercial and industrial situations where there is a lot of foot activity or machinery movement, epoxy grout is frequently used. It offers a strong and long-lasting flooring option for retail establishments, industries, garages, and warehouses.
Tile Installations: In places that require a high level of hygiene and cleanliness, such hospitals, labs, and food processing facilities, epoxy grout is the material of choice for tile installations. Its non-porous structure ensures a sanitary atmosphere by preventing the formation of germs, mould, and mildew.
Swimming Pools and Water Features: Epoxy grout is often used in swimming pools, water fountains, and other water features because of its great resistance to water and chemicals. It contributes to the formation of a watertight seal and offers improved durability against frequent contact with water and pool chemicals.
Kitchen and Bathroom Applications: Epoxy grout is perfect for bathrooms and kitchens where stains and dampness are regular problems. It is used to install tile on bathroom walls, floors, backsplashes and kitchen counters. Epoxy grout is easy to clean and maintain in these places because to its stain-resistance.
Commercial Kitchens and Restaurants: In commercial kitchens and eateries, where the floors and counters are subjected to frequent cleaning and food spills, epoxy grout works effectively. It is a great option for keeping hygiene and fulfilling the criteria of health codes due to its chemical resistance and cleaning simplicity.
Heavy-Duty Industrial Environments: Heavy-duty industrial settings, such as manufacturing plants, auto factories, and warehouses, frequently employ epoxy grout. It is appropriate for environments with machinery and equipment because of its outstanding durability, resistance to chemicals, and capacity to withstand severe loads.
Renovation and Restoration Projects: Epoxy grout is often utilised to strengthen and repair deteriorated or damaged grout lines in remodelling and restoration projects. It contributes to the overall structure’s strengthening and increases the lifespan of tiled surfaces.
These are just a few instances of the numerous uses for epoxy grout. Its adaptability and exceptional qualities make it the go-to option in a variety of sectors where longevity, hygienic design, and durability are crucial.
Also Read: Easy Cement Calculation: How to Calculate 1 Bag (50kg) Cement Volume in CUM CFT Litre?
Cement Grout
Definition and Composition
The main ingredients of cement grout, also known as sanded grout, are cement, water, and sand. It serves as a filler to close cracks and add stability between masonry or tile pieces.
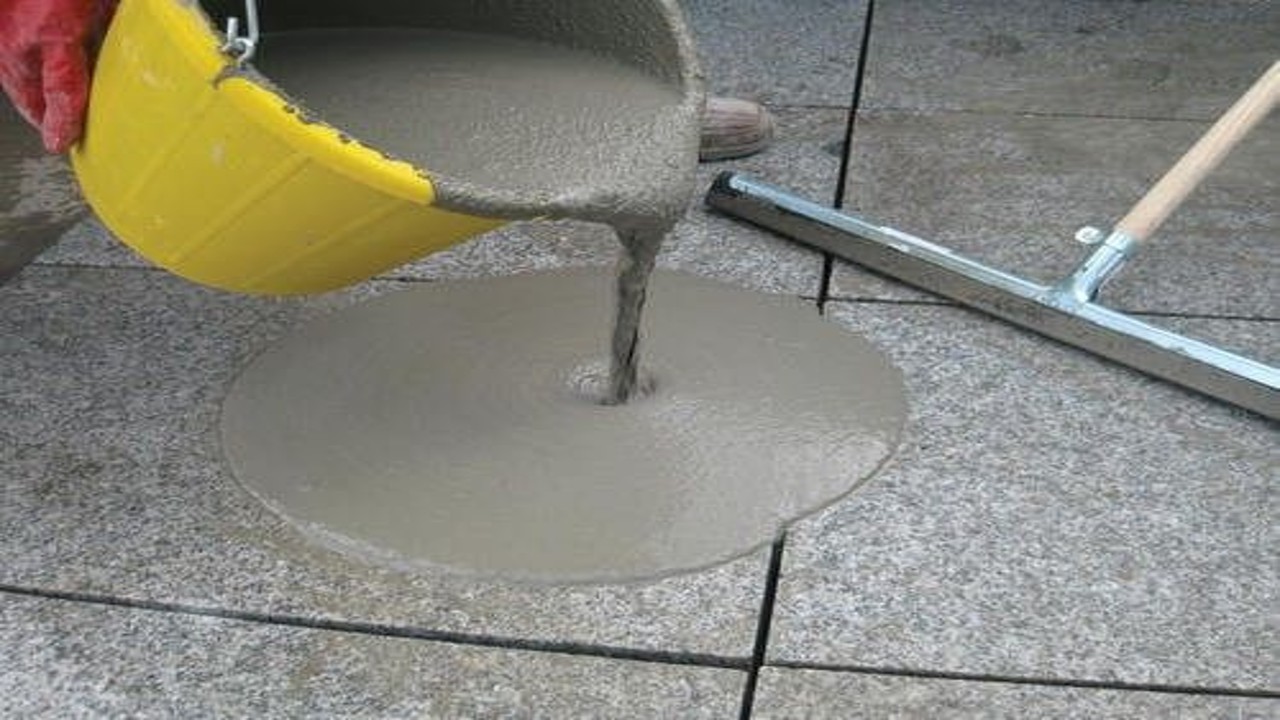
The composition of cement grout involves a few key components:
Cement: The grout mixture’s binding component is cement. Due to its adhesive qualities and capacity to harden when combined with water, Portland cement is frequently utilised.
Water: Since it starts the chemical interaction with cement that leads to the hardening process known as hydration, water is a crucial component of cement grout. For the necessary consistency and strength of the grout to be achieved, the proper water to cement ratio is essential.
Sand: In cement grout, sand is used as a filler ingredient. It usually consists of fine sand or silica sand, which contributes to the mixture’s volume and stability. The sand avoids excessive shrinking during the curing process and adds to the overall strength of the product.
Optional Additives: To improve certain qualities, additives may occasionally be added to cement grout. These additions, which increase flexibility, water resistance, and adhesion, may comprise latex polymers or acrylic modifiers.
Depending on the particular needs of the project and the preferred consistency of the grout, the ratios of cement, water, and sand may change. For the greatest results, it is crucial to adhere to the manufacturer’s instructions and suggested mixing ratios.
Using a grout float or a grout bag, the prepared cement grout mixture is applied to the seams between tiles or masonry units. After wiping away the excess grout, the joints are filled and sealed. The cement grout provides solidity and support to the tiled surface as it hardens and solidifies over time.
Characteristics and Advantages
The material cement grout, which is frequently used in building and civil engineering projects, is a combination of cement, water, and occasionally additives. It has a number of features and benefits that make it a preferred option for many applications. The following are some essential qualities and benefits of cement grout:
Strength and Durability: Because of its great compressive strength, cement grout is well suited for filling holes, fractures, and gaps in buildings. Once it has dried, it solidifies into a tough mass that can sustain masses of weight and extended exposure to the elements.
Flowability: Because cement grout has a fluid character, it may readily flow into tight crevices and difficult-to-reach places. Due to its quality, it may be used for tasks like filling joints in precast concrete elements, sealing cracks in concrete buildings, and grouting below baseplates.
Shrinkage Control: Cement grouts that have been properly prepared can shrink very little after curing. This helps avoid fractures and creates a strong connection between the grout and surrounding surfaces, which is helpful in situations where dimensional stability is essential.
Bonding Strength: Concrete, masonry, steel, and other materials may all benefit from the exceptional bonding abilities of cement grout. When grouting anchors, dowels, and reinforcing bars, this quality is especially advantageous since it improves the system’s overall structural integrity.
Waterproofing and Chemical Resistance: To increase the cement grout’s resistance to moisture and chemicals, additives can be used in the formulation process. This qualifies it for uses like subterranean constructions, swimming pools, and wastewater treatment facilities where waterproofing or resistance to corrosive chemicals are necessary.
Cost-Effective: Comparing cement grout to other grouting materials, it is often more affordable. It is a feasible option for a variety of building projects, from small-scale repairs to significant infrastructure initiatives, thanks to its availability and ease of manufacture.
Versatility: To attain certain qualities, cement grout can be altered by changing the water-cement ratio, adding additives, or employing unique mix patterns. Due to its adaptability, it may be customised to satisfy the needs of various applications, such as non-shrink grouting, anchoring, void filling, and soil stabilisation.
Ease of Application: It is generally simple to apply cement grout since it is made on site and may be pumped or poured into place. It can be installed in tight or challenging locations thanks to its fluid nature and is suitable for both interior and external applications.
Cement grout is an adaptable and dependable material for a variety of building and repair applications due to its qualities and benefits. It is a popular option in the sector due to its strength, durability, flowability, bonding capabilities, and cost efficiency. To achieve the best performance and lifespan, however, it’s crucial to adhere to the correct mixing, positioning, and curing methods.
Also Read: MS Angle Weight Chart PDF: Calculating MS Angle Weight for Accurate On-Site Billing
Applications
Due to its adaptability and useful qualities, cement grout is used in a wide range of building projects. The following are some typical uses for cement grout:
Grouting Under Baseplates: For support and to fill spaces beneath baseplates of structures, such as equipment foundations and column bases, cement grout is utilised. By successfully distributing loads to the underlying soil or substrate, it makes sure that the foundation is strong and sturdy.
Anchoring and Doweling: Anchor bolts, dowels, and reinforcing bars are among the structural components that may be fastened to concrete or masonry with cement grout. It offers a solid connection and supports preserving the stability and integrity of the anchored components.
Void and Crack Filling: The cavities and gaps in concrete and masonry constructions are filled with cement grout. It supports structural integrity restoration, enhances aesthetics, and guards against additional harm or water intrusion.
Joint Filling: The seams between precast concrete components, such as panels, blocks, or tiles, are filled with cement grout. It contributes to the structural continuity, improves the overall visual appeal, and aids in preventing the entry of water and debris.
Soil Stabilization: For soil stabilisation, cement grout is utilised in a variety of settings, such as tunnelling, excavation, and slope stabilisation. It can be put into the ground as an injection to strengthen the soil, decrease permeability, and stop soil erosion.
Waterproofing: To improve its waterproofing abilities, cement grout can be given additives. It is used on buildings like swimming pools, retaining walls, and basements to make a watertight barrier and stop water infiltration.
Repair and Rehabilitation: For the restoration of deteriorating concrete buildings, cement grout is frequently employed. It may be used as a filler for holes, cracks, and spalls to restore structural integrity and lengthen the useful life of the damaged components. It can also be injected into the affected area.
Grouting for Tile Installation: In tile installations, cement grout is used to fill the spaces between tiles, creating a sturdy and attractive surface. It aids in holding the tiles firmly in place, absorbing small movements, and stopping water infiltration.
Underpinning: When underpinning a structure, cement grout is used to reinforce and stabilise the foundation by injecting it into the earth. In order to maintain the structural integrity of settled or weak foundations, it aids in supporting and levelling them.
These are but a handful of the numerous uses for cement grout. It is a useful material for building, repairing, and improving projects due to its adaptability, strength, durability, and bonding qualities.
Cement Mortar
Definition and Composition
By mixing cement, sand, and water in a set ratio, cement mortar is created, which has the consistency of a paste. Building components are joined together with it, gaps are filled, and a smooth, tough surface is produced.
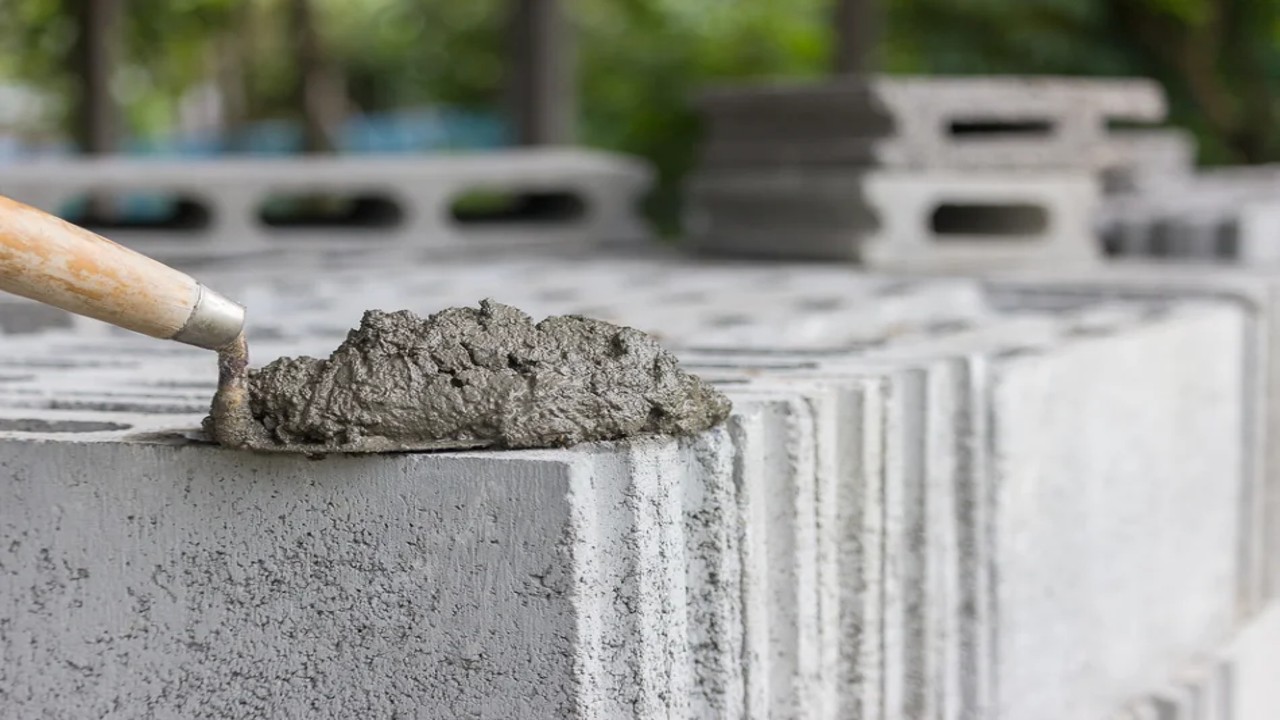
Cement: Cement, which serves as the mortar’s binder, is its main ingredient. Due to its outstanding binding qualities and capacity to harden and acquire strength when combined with water, Portland cement is frequently employed in the manufacture of mortar. Depending on the needs of the project and the particular use, a different type of cement may be utilised.
Sand: The second most important ingredient in cement mortar is sand. It gives the mixture bulk and aids in achieving a workable consistency. Sand for mortar should be properly graded and clean of contaminants like silt and clay. The workability and strength of the mortar are influenced by the sand’s particle size and shape.
Water: Cement must be hydrated in order to harden and become stronger, which requires water. The workability and setting time of the mortar are influenced by the amount of water added to the mixture. To ensure that the cement is properly hydrated, the water utilised should be pure and free of impurities.
Depending on the intended properties of the mortar and the particular application, the ratios of these components can change. In mortar mixtures, the cement to sand ratio is commonly expressed as 1:3, 1:4, or 1:6, denoting the volume or weight proportions of the two materials.
Cement mortar may occasionally contain extra additives or admixtures to enhance particular qualities like workability, water retention, or durability. Plasticizers, air entraining agents, and waterproofing agents are a few examples of these additives.
To ensure that cement mortar performs as intended and has the appropriate strength, it’s crucial to follow suggested mixing techniques and abide by suitable curing methods. Based on project needs, environmental factors, and the type of masonry or finishing work being done, the mortar’s composition should be carefully established.
Characteristics and Advantages
Cement mortar, which is made out of cement, sand, and water, has a number of qualities and benefits that make it a common option in masonry and building applications. The following are some of the salient features and benefits of cement mortar:
Strong Bonding: When masonry pieces like bricks, blocks, or stones are joined together using cement mortar, the connection is strong. It develops a cohesive layer that aids in uniformly dispersing loads and improves the construction’s overall structural integrity.
Good Workability: It is simple to mix, apply, and shape cement mortar to suit a variety of building requirements. It is easy to work with, enabling masons to obtain desired forms and finishes as well as enabling quick and accurate installation.
Durability: Cement mortar offers resilience and long-lasting performance when properly mixed and cured. It may be used both indoors and outside because of its resistance to weathering, temperature fluctuations, and chemical exposure.
Fire Resistance: The ability of cement mortar to withstand fire is helpful in improving the fire safety of buildings. It can affect a building’s overall fire rating and aid in controlling the spread of flames.
Versatility: For a variety of tasks, including masonry work, plastering, rendering, and installing tiles, cement mortar is adaptable and may be employed. It is adaptable to unique project needs and is suitable with a range of building materials.
Cost-Effective: In general, cement mortar is less expensive than other building supplies. Because cement and sand are readily accessible and reasonably priced, cement mortar is a sensible option for many building jobs.
Compatibility: Many various types of finishes, varnishes, and paints are suitable with cement mortar. It offers a good base for further customisation and aesthetic improvement processes like painting, waterproofing, or cladding.
Control over Mix Proportions: With cement mortar, you may easily change the mix proportions to get the desired results. Control over the mortar’s performance is possible by adjusting the cement to sand ratio to maximise workability, strength, or other special needs.
Repairability: Simple maintenance and repair are possible using cement mortar. Mortar joints that are damaged or deteriorated can be changed or repaired, extending the life and maintaining the structural integrity of the masonry structure.
Availability and Familiarity: A common and established building material is cement mortar. It is simple to find and work with because it is widely accessible on the market and well-known among masons and contractors.
Cement mortar is a favoured option for many building applications due to its qualities and benefits. To maintain the required strength, durability, and performance of the mortar, it is crucial to adhere to correct mixing, curing, and application processes.
Applications
Due to its adaptability and advantageous qualities, cement mortar, which is made up of cement, sand, and water, is used in a wide variety of building projects. It is frequently employed for many different things, such as:
Masonry Work: In building, cement mortar is frequently used to lay bricks, blocks, and stones. It serves as a binding agent between the masonry sections, giving the building strength and stability.
Plastering: To provide a smooth and uniform finish, cement mortar is used as a plaster layer on walls, ceilings, and other surfaces. It aids in enhancing the look, safeguarding the supporting surfaces, and serving as a foundation for other ornamental treatments.
Rendering: When rendering a building, a coating of cement mortar is applied to the exterior walls in order to increase insulation, protect against weathering, and enhance the structure’s looks.
Pointing and Repointing: Pointing, the technique of filling and completing the joints between masonry units, uses cement mortar. It strengthens the joints, increases water resistance, and improves the structure’s general look. Repointing entails removing and replacing mortar joints that have deteriorated or been damaged.
Tile Installation: Tiles, such as ceramic or stone tiles, are fixed to walls and floors using cement mortar. It ensures stability and longevity by creating a solid link between the substrate and the tiles.
Stucco Work: For stucco applications, which entail painting a decorative and protective covering on external walls, cement mortar is used. To create the desired appearance, it can be textured or treated in a variety of ways.
Parging: The outer surfaces of foundation walls are parged with cement mortar. It contributes to better insulation, increased aesthetic appeal, and moisture protection for the foundation.
Repair and Patching: Concrete or masonry components that have been damaged or degraded can be repaired and patched using cement mortar. It is used to fill cavities, fissures, and spalls, restoring the surfaces’ structural integrity and aesthetic appeal.
Bedding for Pavers and Slabs: Pavers, slabs, and other paving pieces are laid on top of a bed of cement mortar. It contributes to the creation of a flat surface, offers stability, and prevents moving.
Sculpting and Artwork: For the purpose of creating artistic and ornamental components, such as sculptures, decorations, and architectural details, cement mortar can be moulded and moulded.
These are but a handful of the numerous uses for cement mortar. It is a useful material in a variety of building, repair, and finishing jobs due to its adaptability, bonding strength, longevity, and simplicity of use.
Key Differences
Here are the key differences between epoxy grout, cement grout, and cement mortar:
Composition:
- Epoxy Grout: Epoxy resin, hardener, and fillers.
- Cement Grout: Cement, sand, and water.
- Cement Mortar: Cement, sand, and water.
Durability:
- Epoxy Grout: Highly durable, resistant to stains, chemicals, and moisture.
- Cement Grout: Relatively durable, but not as resistant to stains and chemicals as epoxy grout.
- Cement Mortar: Offers good durability but may be more prone to deterioration over time compared to epoxy grout.
Water Resistance:
- Epoxy Grout: Non-porous and highly water-resistant.
- Cement Grout: Porous and may absorb water over time, requiring sealing.
- Cement Mortar: Porous and may absorb water, requiring additional waterproofing measures for specific applications.
Stain Resistance:
- Epoxy Grout: Highly stain-resistant.
- Cement Grout: Less stain-resistant and may require sealing to prevent staining.
- Cement Mortar: Can be prone to staining, especially if not properly sealed or maintained.
Flexibility:
- Epoxy Grout: Offers some flexibility, allowing for slight movement without cracking.
- Cement Grout: Limited flexibility and may crack under excessive movement.
- Cement Mortar: Rigid and less flexible, making it more susceptible to cracking.
Adhesion:
- Epoxy Grout: Excellent adhesion properties, providing a strong bond between tiles and substrates.
- Cement Grout: Good adhesion but not as strong as epoxy grout.
- Cement Mortar: Strong bonding properties, providing stability between masonry units.
Cost:
- Epoxy Grout: Generally more expensive than cement grout and cement mortar.
- Cement Grout: More cost-effective compared to epoxy grout.
- Cement Mortar: Generally more cost-effective than both epoxy grout and cement grout.
Applications:
- Epoxy Grout: Preferred for areas with high moisture, such as showers, swimming pools, and spas, where stain resistance and durability are crucial.
- Cement Grout: Commonly used for masonry work, joint filling in tile installations, and general construction projects.
- Cement Mortar: Primarily used for masonry work, plastering, rendering, and repair applications.
It’s important to consider the specific requirements of each project and consult with professionals to determine the most suitable grouting or mortar option based on factors such as the application, environment, aesthetics, and budget.
Conclusion
Finally, it should be noted that each of the cement mortar, epoxy grout, and cement grout has particular properties and uses. Epoxy grout is ideal for difficult situations because of its superior durability, chemical resistance, and design flexibility. The most practical, affordable material for most tiling applications is cement grout. For masonry building, cement mortar is necessary because it offers powerful adhesion. Builders and homeowners may select the best material for their projects by taking into account each material’s unique features.
Frequently Asked Questions – FAQs
Can epoxy grout be used for outdoor applications?
Since epoxy grout can fade when exposed to UV rays, it is often not advised for outdoor usage. It works well inside or in locations with little exposure to sunlight.
Is cement grout waterproof?
Not by nature, cement grout is not waterproof. Nevertheless, it may be improved by using grout sealers to increase its water resistance and safeguard it from stains.
Can cement mortar be used for tile installation?
It is not normally advised to install tiles using cement mortar because it is primarily used for masonry building. For attaching tiles to surfaces, thinset mortar is a better choice.
How long does epoxy grout take to cure?
Depending on the particular product and environmental factors, epoxy grout might take a different amount of time to cure. It is crucial to adhere to the manufacturer’s recommendations for the suggested curing period.
Can cement grout be applied over existing grout?
It is occasionally feasible to add fresh cement grout on top of old grout. Before applying the new layer, it is crucial to make sure the old grout is clean, in good condition, and well prepared.